■固定概念の恐ろしさ
どのような事柄にも「固定概念」が存在します。風習、慣習、文化、経験、教育、生い立ちなど固定概念を生む要因は様々です。固定概念は、複数の人が物事を同時に考える際の一定の基準・土台になり、検討をスムーズに進める役割もあります。
しかしながら、物事を改善しようとする場合においては、大きな壁として立ちはだかります。我々、企業支援を生業とする立場としては、恐ろしく高い壁になり、その壁をこじ開けるのは決して容易ではありません。
「何も知らないのに何が分かる」
「これはこういうものだ」
「既にそれはやって無理だった」
こんなセリフが良くでますし、口に出さずとも内心ではそう思っている場合が多くあります。こうなると、どんなに提案をしても、それが実行に移される事は殆どありません。
■固定概念を打ち破るには
私は「客観的な数値データ」しかないと考えています。正しく集計されたデータは嘘をつきません。”データが嘘をつかない事実” を知らない人には効果がありませんが、殆どの人には効果的です。
それにも関わらず、数値データを持っていない経営者が多すぎます。
<飲食店の例>
- 時間ごとの来店客数、客属性
- メニュー毎の注文数、客属性(性別、年齢、職業、家族構成)
- メニュー毎の原価
- 天候による来店数、注文数、注文メニューの変動
何となくは分かっていても、数値データにすると“思い込み”だった事に気付いたり、新しい発見・問題点が見つかったりします。
■ものづくり改善における数値
とある製造現場の改善で、ビデオ撮影による時間分析をしました。同じ構成のラインが2ラインあり、1日10品種を生産しています。
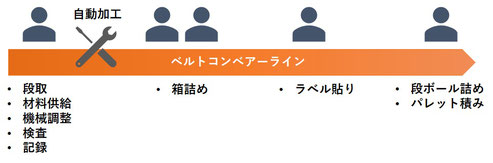
全く同じ構成のラインが2ラインあり、5人×2ラインで10名が作業しています。
先頭にオペレーターと呼ばれる、ラインを動かす人がいます。
このオペレーターに着目しました。オペレーターの作業をビデオによる定点観測したところ、次のような作業比率になりました。
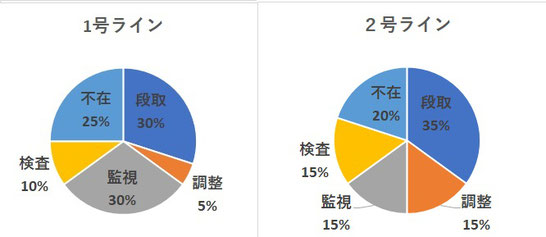
<1号ラインと2号ラインの差>
1号と2号では全くラインの構成が同じにも関わらず、作業比率に差がある事が分かりました。その要因は、人の熟練度ではなく、機械にありました。1号ラインは3年前に新設、2号ラインは10年前に作った古い設備で、基本的な構造こそ一緒ですが、部品の摩耗やガタで安定していませんでした。
<正味作業比率>
オペレーターで言う正味作業比率は、「段取」「調整」の2つです。この2つをしなければ機械は動きませんが、その他の作業はしなくても機械は動きます。
1号ラインは正味作業比率は35%、2号ラインは50%です。
■改善提案
この数値データをもとに次のような提案をしました
- 2号ラインのオーバーホール
- 検査表記入作業の電子化
- 不在時の作業分解(今やるべき事と、後からで良い事をわける)
- 段取待ちにならないような生産計画作り
現時点で正味作業比率は35%+50%=85%で、100%を超えません。
1人削減できるのではないか?と疑問を持ちますが、「検査」も含めると100%を超えてしまします。
そこで、「1.」「2.」にて正味作業と検査の時間を下げてやる必要があります。
そして「3.」にて不在の時間も削減します。
さらには、「4.」にて段取作業が交互になるような生産計画を提案し、実際に計画書案を提示しました。
■推進力
この提案をした際、あるベテラン社員が一言。
「オペレーターを減らすのは無理です」
この一言で、全ての改善は終わりました。
本当に難しければ「○○すればできる」「□□をやめればできる」という条件出しが改善の糸口になるものです。しかし、頭から諦めてしまったら何も生まれません。
結果的には、上司が
「数値上は出来るはずなんだから、何が問題なのかもう一度考えなさい」
と指示をしたことで、前に進みだしました。
こうした前向きな管理者・経営者がいる会社は、改善ができると思います。
固定概念の怖さを伝える為に、長い文章になってしましたが、どうしたらできるのか?常に考える事が、改善の推進力になると思います。
今まで通りでいい、これがベスト、改善はやり尽くした、こんな考えを持たないで欲しいと思います。
コメントをお書きください